Technology meets tradition.
Have you heard of X-Ray diamond sorting? If not, be my guest and travel behind the scenes to an alluvial diamond-mining operation overseen by our friends at Alrosa. They have provided an amazing video example of this efficient method of separating the wheat from the chaff, as it were.
Traditional sorting and separating of diamond-bearing ore has been done by grease-belt and exhaustive human hand-labor. With that said, check out this amazing 2016 video (thank you for this, Alrosa).
Here’s how it works
1. Diamond bearing ore is transported from aggregation at the mine’s source for processing.
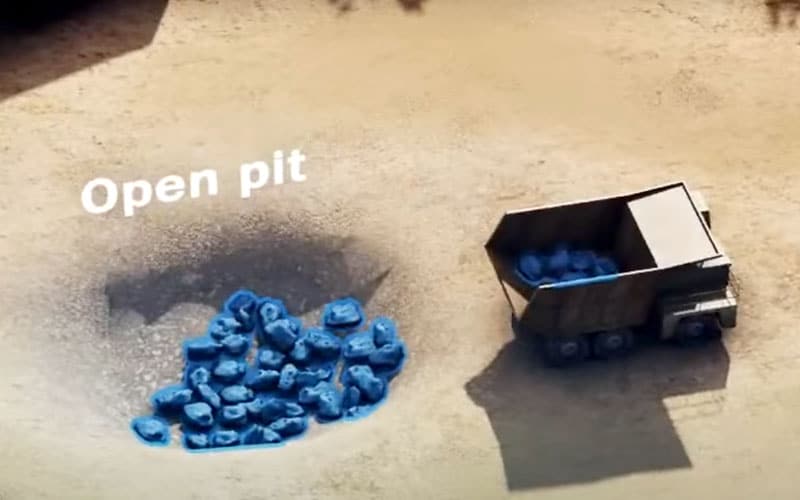
2. The ore is crushed to smaller, manageable sizes (Alrosa calls the process ‘crashing’ instead of crushing and I am good with that).
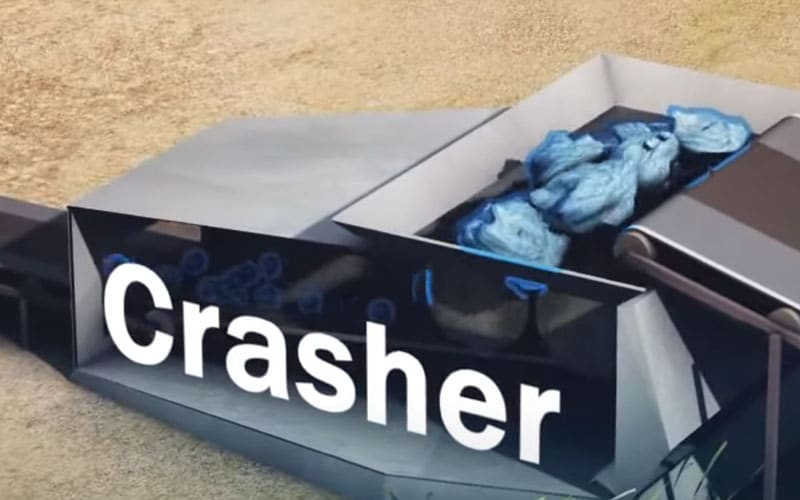
3. The crushed ore is separated into lighter and heavier material through a process called dense media separation, which effectively brings the most likely diamonds to the front of the line.
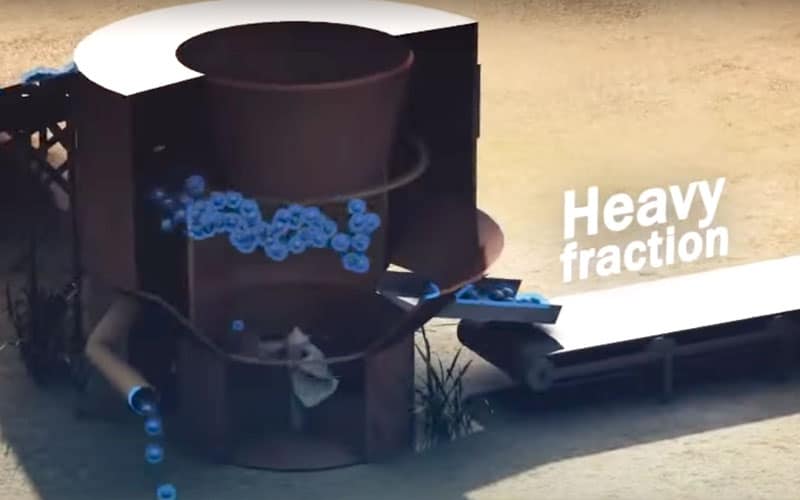
4. Pieces of ore are dropped in front of X-Ray emitters and photomultipliers. Why? Because diamond reacts to X-Rays, which triggers a response in the photomultiplier, at which point a puff of air redirects any diamond-bearing ore into a collection bin.
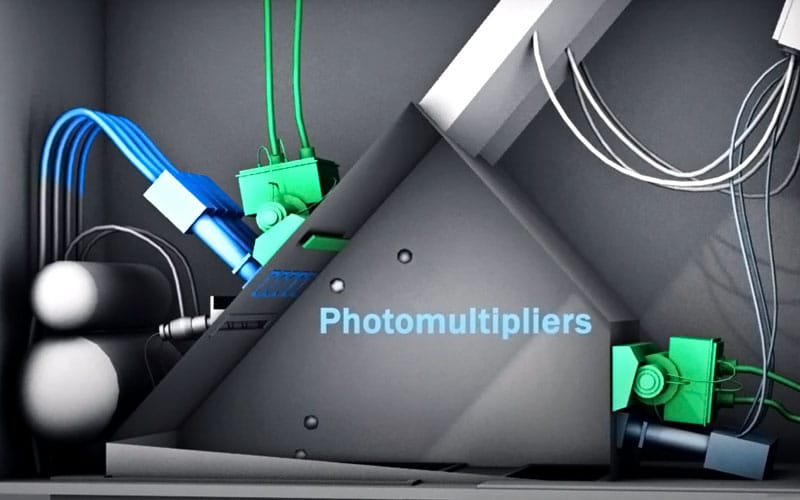
In this manner, the material containing diamonds becomes concentrated and separated from “tailings,” meaning non-diamond bearing ore, which will become returned to the mining sites during rehabilitation.
I find the entire process, from extraction to processing to separation, to be fascinating. But don’t take my word for it. Scroll up and watch the video.
It’s a nice example of modern technology applied to a traditional industry dealing in billions-years old material. Pop some popcorn (but don’t let those X-Rays knock any kernels away from you!) and enjoy.